Problemler ve Çözümleri
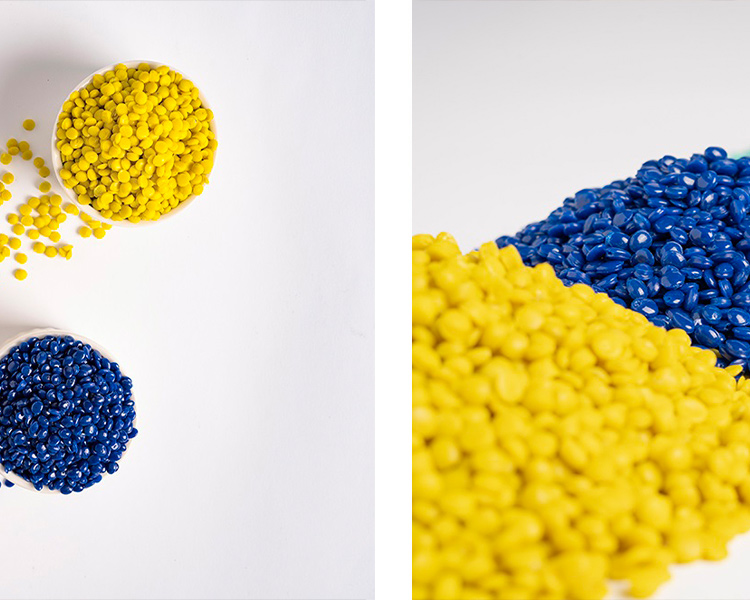
Siyah Noktalar
Makinada:
- Gramajı çok yüksek olabilir.
- Çok uzun sürede kapalı kalmış olabilir.
- Kovan iyi temizlenmemiş olabilir.
- Doğru meme kullanılmamış olabilir.
Kalıpta:
- Ölü köşeleri olan yolluk
Hammaddede:
- İçinde karışık başka mal olabilir
- İçindeki başka mal yanabilir
Çözümleri Sırayla:
- Makine aynı sıcaklıkta doğru malla temizlenmeli.
- Başka mal karışıp karışmadığı kontrol edilmeli.
- Yolluk girişleri ve tipi kontrol edilmeli.
- Filtrenin delinmesi kontrol edilmeli.
Hava ve Gaz Kabarcıkları
Makinada:
- Enjeksiyon basıncı çok düşük olabilir.
- Geri akış valfi arızalı olabilir.
- Geri emiş çok uzun olabilir
- Erime işlemi çok hızlı olabilir.
- Huni girişinde hava sıkışmış olabilir.
- Kötü besleme olabilir.
Kalıpta:
- Kalıp sıcaklığı düşük olabilir.
- Kalıp gaz çıkışı kapalı olabilir.
- Parçanın yolluk girişi et kalınlığı.
- İnceden kalına doğru olabilir
Hammaddede:
- Malzeme yüksek sıcaklığa dayanamıyor olabilir.
Çözümleri Sırayla:
- Enjeksiyon basıncı ve ütüleme basıncı artırılmalı.
- Geri basıncı artırılmalı.
- Kalıp sıcaklığı artırılmalı.
- Geri akış valfi kontrol edilmeli.
- Kalıp hava kanalı kontrol edilmeli.
- Yolluk çapı artırılmalı.
Akış İzi
Makinada:
- Enjeksiyon hızı çok düşük veya yüksek olabilir.
- Enjeksiyon basıncı çok düşük olabilir.
- Ütüleme basıncı çok düşük olabilir.
Kalıpta:
- Kalıp ısı kontrolü iyi değildir.
- Kalıp sıcaklığı yolluk girişinde çok yükse olabilir.
- Kalıp çok soğuk olabilir.
- Yolluk çapı çok küçük olabilir.
- Yanlış yolluk girişi
- Yanlış sıcak yolluk sistemi
Hammaddede:
- Malzeme sıcaklığı düşük olabilir
Çözümleri Sırayla:
- Enjeksiyon hızı ayarlanmalı.
- Erimemiş mal olma ihtimali kontrol edilmeli.
- Enjeksiyon çukuru kontrol edilmeli.
Yüzeyde Yanıklar (Dizel Effect)
Makinada:
- Geri akış valfi arızalı olabilir.
- Enjeksiyon hızı çok hızlı çok yüksek olabilir.
- Geri basınç çok yüksek olabilir.
Kalıpta:
- Hava çıkış kapalı olabilir.
- Kalıptaki keskin köşelere bağlı yanma.
- Yolluk girişi dar olabilir.
Hammaddede:
- Malzeme yüksek sıcaklığa bağlı olarak yanabilir veya düşük sıcaklık nedeniyle sürtünerek yanabilir.
Çözümleri Sırayla:
- Hava emiş kanallarının tıkanıp tıkanmadığı kontrol edilmeli.
- Enjeksiyon hızı düşürülmeli.
- Enjeksiyon basıncı düşürülmeli.
- Kademeli enjeksiyon denenmeli.
- Isıtıcıların doğru çalışıp çalışmadığı kontrol edilmeli.
- Vida hızı düşürülmeli.
- Meme sıcaklığı düşürülmeli.
Parça Soyulma
Makinada:
- Enjeksiyon hızı çok yüksek olabilir.
Kalıpta:
- Kalıp çok soğuk olabilir.
- Yollukta keskin köşeler olabilir.
- Keskin köşelere bağlı yüksek ısı oluşması.
Hammaddede:
- Malzeme eriyik sıcaklığı çok yüksek olabilir.
- Malzeme tam erimemiş olabilir.
- Başka bir polimer katılmış olabilir.
- Çok fazla deşe veya kırılmış mal karışması olabilir.
Çözümleri Sırayla:
- Eriyik sıcaklığı arttırılmalı.
- Kalıp sıcaklığı arttırılmalı.
- Enjeksiyon hızı düşürülmeli.
- Masterbatch değişmeli.
- Deşe veya kırık oranı düşürülmeli.
- Malzeme veya kurutma kontrol edilmeli.
- Keskin köşelere radius verilmeli.
Ebatlarda Farklılık
Makinada:
- Enjeksiyon basıncı çok düşük olabilir.
- Ütüleme süresi çok düşük olabilir.
- Çevrim süresi düşük olabilir.
- Isıtıcılar arızalı olabilir.
- Geri akış valfi arızalı olabilir.
Kalıpta:
- Kalp sıcaklığı çok yüksek olabilir.
- Yolluk girişleri çok küçük olabilir.
- Kalıp çok küçük olabilir.
Hammaddede:
- Yanlış malzeme seçilmiş olabilir.
Çözümleri Sırayla:
- Eriyik sıcaklığı arttırılmalı.
- Kalıp sıcaklığı arttırılmalı.
- Enjeksiyon hızı düşürülmeli.
- Çevrim süresi iyileştirilmeli.
- Yolluk çağı arttırılmalı.
- Cam Elyaflı mallarda yolluk girişi değiştirilmeli.
Çapak
Makinada:
- Kapama basıncı düşük olabilir.
- Enjeksiyon basıncı yüksek olabilir.
- Enjeksiyon hızı çok yüksek olabilir.
Kalıpta:
- Kalıp yanlış bağlanmış olabilir.
- Kalıp yüzeylerinde aşınma, bozulma olabilir.
- Kalıp yüzeyi büyük olabilir.
Hammaddede:
- Malzeme sıcaklığı yüksek olabilir.
- Malzeme akışkanlığı çok yüksek olabilir.
Çözümleri Sırayla:
- Enjeksiyon hızı düşürülmeli.
- Enjeksiyon basıncı düşürülmeli.
- Kapama Kuvveti arttırılmalı.
- Eriyik sıcaklığı düşürülmeli.
- Kalıp sıcaklığı düşürülmeli.
- Kapama kuvveti arttırılmalı.
Parça Yüzeyinde Akış izleri
Makinada:
- Enjeksiyon hızı çok yüksek olabilir.
Kalıpta:
- Kalıp çok soğuk olabilir.
- Yolluk çapları çok düşük olabilir.
- Yanlış yolluk girişi.
Hammaddede:
- Malzeme erimiş olabilir.
Çözümleri Sırayla:
- Enjeksiyon basıncı arttırılmalı.
- Meme Isıtıcı kontrol edilmeli.
- Kalıp sıcaklığı arttırılmalı.
- Eriyik sıcaklığı arttırılmalı.
- Yolluk çapı büyütülmeli.
- Yolluk girişi değiştirilmeli veya direk giriş yapılmalı.
Parça Yüzeyinde Yuvarlak Halkalar
Makinada:
- Enjeksiyon hızı çok düşük olabilir.
- Enjeksiyon basıncı çok düşük olabilir.
Kalıpta:
- Kalıp sıcaklığı çok düşük olabilir.
- Kalıp yüzeyinde farklı desen olabilir.
Hammaddede:
- Malzeme eriyik sıcaklığı düşük olabilir.
Çözümleri Sırayla:
- Enjeksiyon hızı arttırılmalı.
- Enjeksiyon basıncı arttırılmalı.
- Eriyik sıcaklığı arttırılmalı.
- Kalıp sıcaklığı arttırılmalı.
- Kalıp deseni kontrol edilmeli.
Kalıba Yapışma (Dişi Kalıba)
Makinada:
- Enjeksiyon basıncı çok yüksek olabilir.
- Enjeksiyon hızı çok yüksek olabilir.
- Ütüleme süresi çok uzun olabilir.
- Mal alımı çok fazla olabilir.
Kalıpta:
- Kalıp sıcaklığı çok yüksek olabilir.
- Kalıp çok soğuk olabilir.
- Kalıp yüzey deseni kötü olabilir.
Hammaddede:
- Meme sıcaklığı çok yüksek olabilir.
Çözümleri Sırayla:
- Çevrim süresini kontrol edilmeli. (Soğuma)
- Enjeksiyon basıncı düşürülmeli.
- Ütüleme süresi düşürülmeli.
- Enjeksiyon hızı düşürülmeli.
- Sabit yastıklama için mal alımı ayarlanmalı.
- Kalıp yüzeyi kontrol edilmeli.
- Kalıp açma süresi arttırılmalı.
- Malzeme sıcaklığı düşürülmeli.
- Kalıp sıcaklığı düşürülmeli.
- Doğru kalıp ayırıcı kullanılmalı.